-
Flexo Folder Gluer
-
Automatic Folder Gluer
-
Box Folder Gluer Machine
-
Flexo Printer Slotter
-
Flexo Printing Slotting Machine
-
Carton Making Machine
-
Corrugated Box Printing Machine
-
Corrugated Box Die Cutting Machine
-
Semi Automatic Box Stitching Machine
-
Automatic Strapping Machine
-
Flute Laminator Machine
-
Cardboard Production Line
-
Jordan CustomerThe machine not have any big shutdown since so many years, it's very stable and cost save.
-
Thailand CustomerThe machine running very well till now, and service is good, we would like to work with them again, thank you!!!
-
Malaysia CustomerWithin last 2.5 years, we bought 3 machine from Toprint, they deserved our trust and we would like to work with them for long terms.
Corrugated Cardboard Production Line 5.5KW 5 Layer 300m/Min
Place of Origin | foshan.CN |
---|---|
Brand Name | StarPack |
Certification | Patent Certificate, CE Certificate |
Model Number | XHL350 |
Minimum Order Quantity | 1 Set |
Price | Negotiation |
Packaging Details | Steel Base with Carton Boxes and Film Wrapping |
Delivery Time | 120-160 days |
Payment Terms | L/C, T/T |
Supply Ability | 3 Sets per Month |
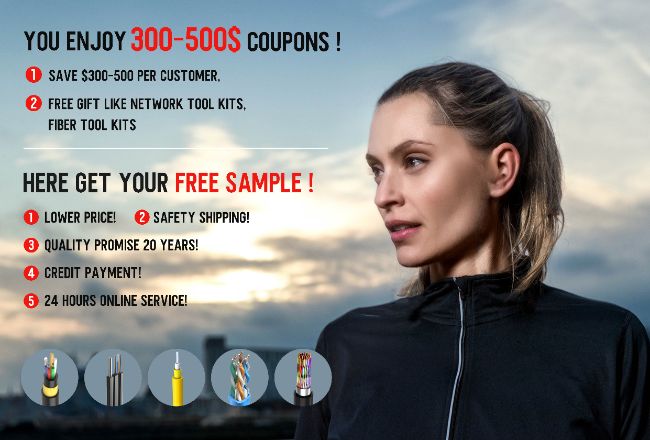
Contact me for free samples and coupons.
Whatsapp:0086 18588475571
Wechat: 0086 18588475571
Skype: sales10@aixton.com
If you have any concern, we provide 24-hour online help.
xName | Cardboard Production Line, Corrugated Cardboard Making Machine, Corrugating Cardboard Production Line | Voltage | 380V 50HZ Or Custom |
---|---|---|---|
Type | Automatic High Speed | Port Of Loading | Guangzhou Or Shenzhen China |
Condition | Brand New | ||
Highlight | 5.5KW Cardboard Production Line,300m/min Cardboard Production Line,Corrugated Cardboard Making Machine |
High speed corrugated paper board production line. Corrugated board production line 5-layer cardboard. Production line for 5-layer cardboard paper sheet. 5-layer corrugated paper board production line.
Features
- This single facer adopts glue tray free design. The gluing roller’s rotation direction is inversed with the traditional single facer. By adopting this design, the extra glue won’t splash out and waste. Moreover, for traditional single facer, the corrugated roller is closed to the glue which is easily to broil the glue, lead to waste.
- Single facer adopts servo motor which is the unique variable speed drive mode of the XHL factory to remove gear energy consuming. The main motor adopts synchronous belt direct drive mode and cooperates with the self-developed patent design, which saves more than 30% electricity compared with traditional single facer.
- When the traditional corrugating single facer machine stops operation, the rolles will stop rotation and cause the temperature is uneven between top and bottom. We called “banana effect”, which means when re-production, foaming created, produce the waste, and slow down the line speed. The XHL350 High speed corrugating machine newly developed by our factory which can automatically separates the light pressure roller and the corrugating roller when machine stop operation, while all the roller can rotate independently at the same speed in order to reach the temperature average effect. When re-start the machine, the paper board won’t become out of shape and cave in due to uneven temperature of corrugated roll, greatly reducing the waste.
- The First Patented Design – Front Push Type to change corrugated roller in 20mins, makes production more flexible.
- Regarding the actual opeation effect of the negative pressure design and the positive pressure design, XHL350 adopts negative pressure design which allows to rapid acceleration or sudden braking and will not produce waste products; paper is easy threading, safe & simple. The current market generally adopts positive pressure design. The disadvantages are that the corrugated roller creates hot air which will blow out, so that the working environment temperature is high; the rapid acceleartion and sudden braking are easy to produce waste products; threading not convenient, it’s troublesome once paper braking and roll up into bellows;complicated components, high maintenance cost.
- The operation console is integrated with the machine body which is simple & practical, makes workers’ operation reaction being quicker, saving more space.
Technical Parameters
01 | Max mechanical speed | 350m/min |
02 | Max production speed | 300m/min |
03 | Corrugated roller diameter | Ф408mm |
04 | the upper and the lower roller both made of high-quality chrome molybdenum alloy steel, combined treatment to strengthen the hardness, surface is applied tungsten carbide coating, the service life is guaranteed 30,000,000 meters. Pressure roller diameter Ф408mm, surface is grinded and hard chrome plated. Pre-heater roller diameter Ф500mm, surface is plated. Gluing roller diameter Ф320mm, surface is grinded with concave and hard chrome plated. Glue control roller diameter Ф196mm, surface is grinded polish and hard chrome plated. All rolls inside the machine are precious balance treated | |
05 | FRA "Schneider" electric apparatus | |
06 | Servo motor | |
07 | Taiwan oil hydraulic system, hydraulic pressure station | motor 5.5KW |
08 | Taiwan"Chengbang" reducer motor | |
09 | "AIRTAC" pneumatic components | |
10 | Electric cabinet with industrial air conditioning | |
11 | Roller changing within 10 mins |